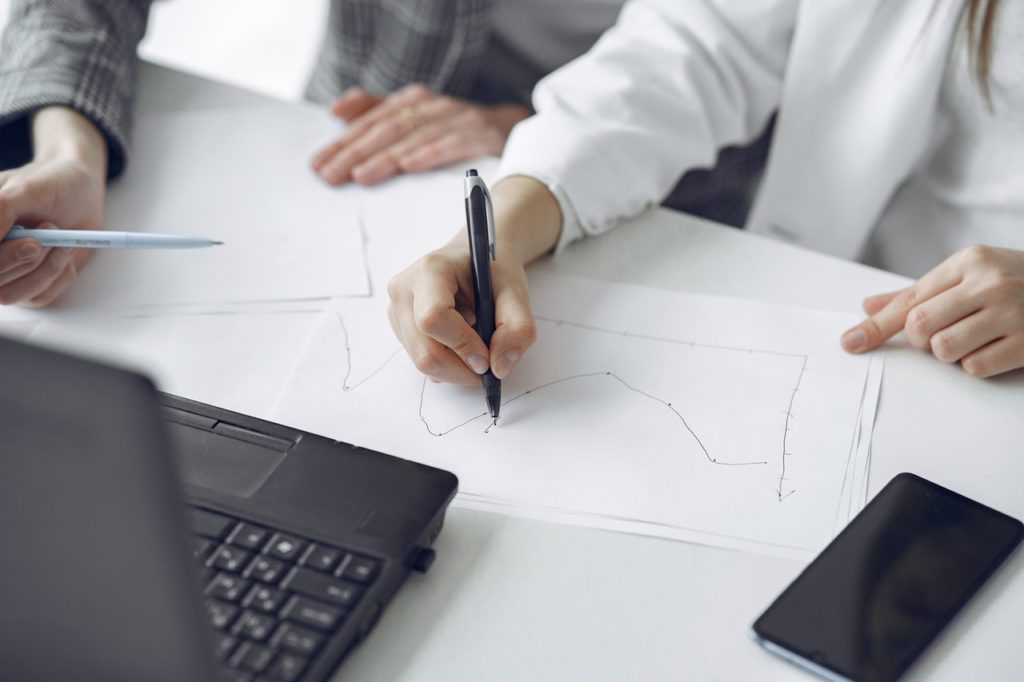
L’MRP è nato come MRP I (materials requirements planning) attorno agli anni sessanta. Allora era considerato un metodo di esplosione dei fabbisogni di materiali vari. La distinta base, che rappresenta il legame tra i materiali e il prodotto, attraverso l’MRP permetteva di calcolare il numero di componenti necessari per realizzare una certa quantità di prodotto finito. Negli anni settanta ci si rese conto che lo strumento si poteva evolvere per diventare capace di gestire le priorità e i tempi di produzione. Si pervenne a formulare in quegli anni la teoria della schedulazione (theory of scheduling) che rappresenta ancora oggi un punto di riferimento costante nel campo della gestione della produzione. Il sistema MRP I è lo strumento che permette di tenere sotto controllo produzione, fornitori, terzisti, allo scopo di consentire una lineare gestione dei materiali; inoltre sviluppa un piano di produzione allo scopo di assicurare la disponibilità dei materiali, dei componenti e dei semilavorati per rispettare assetto, processo e risultato del piano di produzione (fino alle consegne). Negli anni ottanta si è sviluppato l’MRP II: dall’inglese “manufacturing resources planning” per stigmatizzare che la pianificazione non riguarda solo i materiali (organizzazione produttiva degli approvvigionamenti), ma tutte le risorse che si trovano lungo il corso di tutto il processo produttivo. Pertanto l’MRP II è diventato uno strumento di di decision-making globale per qualsiasi azienda di produzione.
Mentre l’MRP I è un metodo “push”, in quanto spinge la produzione da monte a valle, l’MRP II può essere considerato (come il kanban) un metodo “pull”, trainante la produzione da valle a monte. Ad esempio esistono due reparti (1 e 2) che costituiscono due fasi successive di produzione. Se l’iniziativa viene presa dal reparto 1 e il reparto 2 la subisce, si ha un metodo push, viceversa se l’iniziativa viene presa dal reparto 2 e il reparto 1 la subisce si ha un metodo pull. L’esempio più classico di metodo pull si ha nel kanban, ove un banale cartellino invertito sui contenitori, mediante spostamento da quello pieno a quello vuoto, sostituisce l’ordine di acquisto o di produzione, in quanto accompagna sempre il contenitore vuoto (da riempire di pezzi). Il codice del contenitore vuoto costituisce un ordine di acquisto di materie e/o componenti, oppure un ordine di produzione impartito ad un reparto a monte da parte di un reparto situato a valle del medesimo.
L’MRP ingloba in sé, oltre alla funzione di gestione dei materiali, la schedulazione e la gestione produttiva e/o distributiva.